In high-precision manufacturing, where even minor project delays or missteps can lead to massive financial losses, the pressure to equip new engineers with real-world project management skills is immense. Traditional onboarding models: manuals, classroom instruction, and shadowing senior team members, often fail to prepare employees for the complexities of actual project execution.
Jacob Carter, Director of Learning & Development at a Texas-based manufacturing company, faced this exact challenge. His team followed a structured yet passive training approach, but new engineers struggled when it came time to manage real project timelines, make decisions under pressure, or coordinate across functions.
Let’s see how Jacob turned things around with the help of an immersive, hands-on project management training platform.
The growing challenge of training engineers in high-precision manufacturing
Jacob’s company was a major player in precision manufacturing, producing aerospace components where millimeter-level accuracy was critical.
Jacob’s onboarding process for new engineers followed a traditional approach of four weeks of classroom instruction, technical manuals on machine operations, and job shadowing with experienced engineers.
Jacob’s onboarding process for new engineers followed a traditional approach of four weeks of classroom instruction, technical manuals on machine operations, and job shadowing with experienced engineers.
While this method had worked in the past, as technology advanced and machines became more complex, training gaps widened.
New engineers struggled to transition from theory to real-world execution, and mistakes on live production lines led to costly delays.
When theory fails: the costly consequences of inadequate project management training
Shortly after onboarding, a new project engineer was assigned to co-lead a time-sensitive manufacturing initiative, delivering critical aerospace components to a high-profile client. The engineer had completed classroom training, understood the steps, and had shadowed senior project leads.
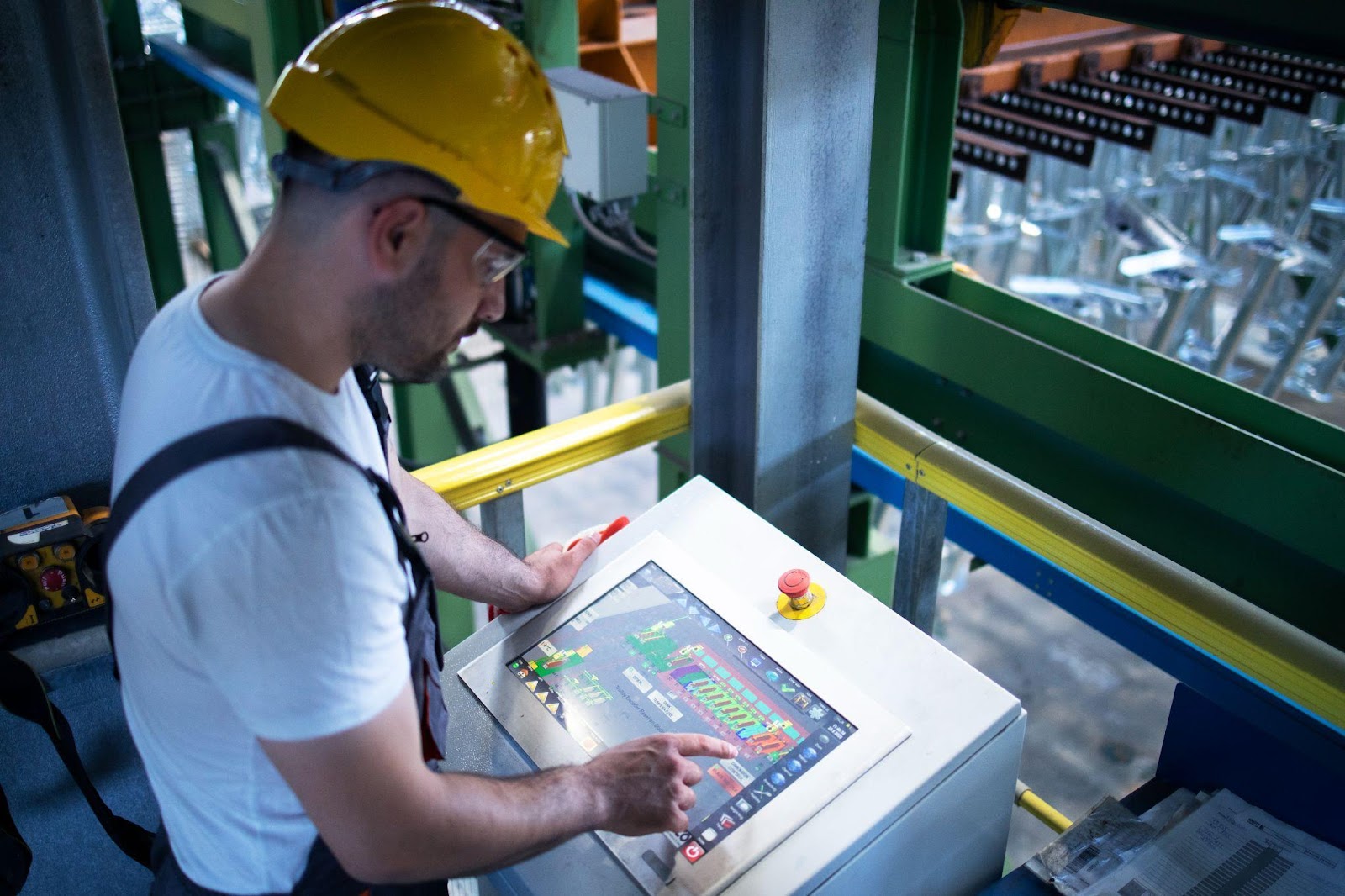
But when it came time to create the project timeline, assign resources, and manage cross-functional coordination, critical delays occurred. A missed procurement deadline caused a bottleneck, pushing production back by two weeks.
The outcome: a $100,000 client penalty for late delivery, damaged trust, and a leadership review of the training process. Jacob Carter, Director of Learning & Development, faced hard questions. How could someone trained in the system still make such avoidable errors?
The issue wasn’t knowledge, it was a lack of practical project experience. The engineer had never practiced managing dependencies, handling unexpected delays, or presenting progress updates under pressure.
Jacob’s analysis revealed a deeper flaw in the project management training:
- Training was too theoretical and compliance-focused: While engineers understood concepts, they lacked the skills to apply them under real project pressures.
- No alignment with business outcomes: Training didn’t reflect the urgency, complexity, or cross-functional nature of live manufacturing projects.
- Dry content led to poor engagement and retention: Manuals and passive learning failed to keep new hires actively involved or mentally prepared for on-the-job challenges.
- Shadowing lacked ownership: Watching experienced engineers helped with exposure, but didn’t offer a space to make decisions or learn from mistakes.
- Effectiveness was hard to measure: There were no clear KPIs or performance benchmarks to assess whether training translated to job readiness.
Jacob needed more than just content, he needed a way to build true project readiness, align training with business outcomes, and quantify its impact on performance.
A game-changing solution: SPL’s immersive project management training
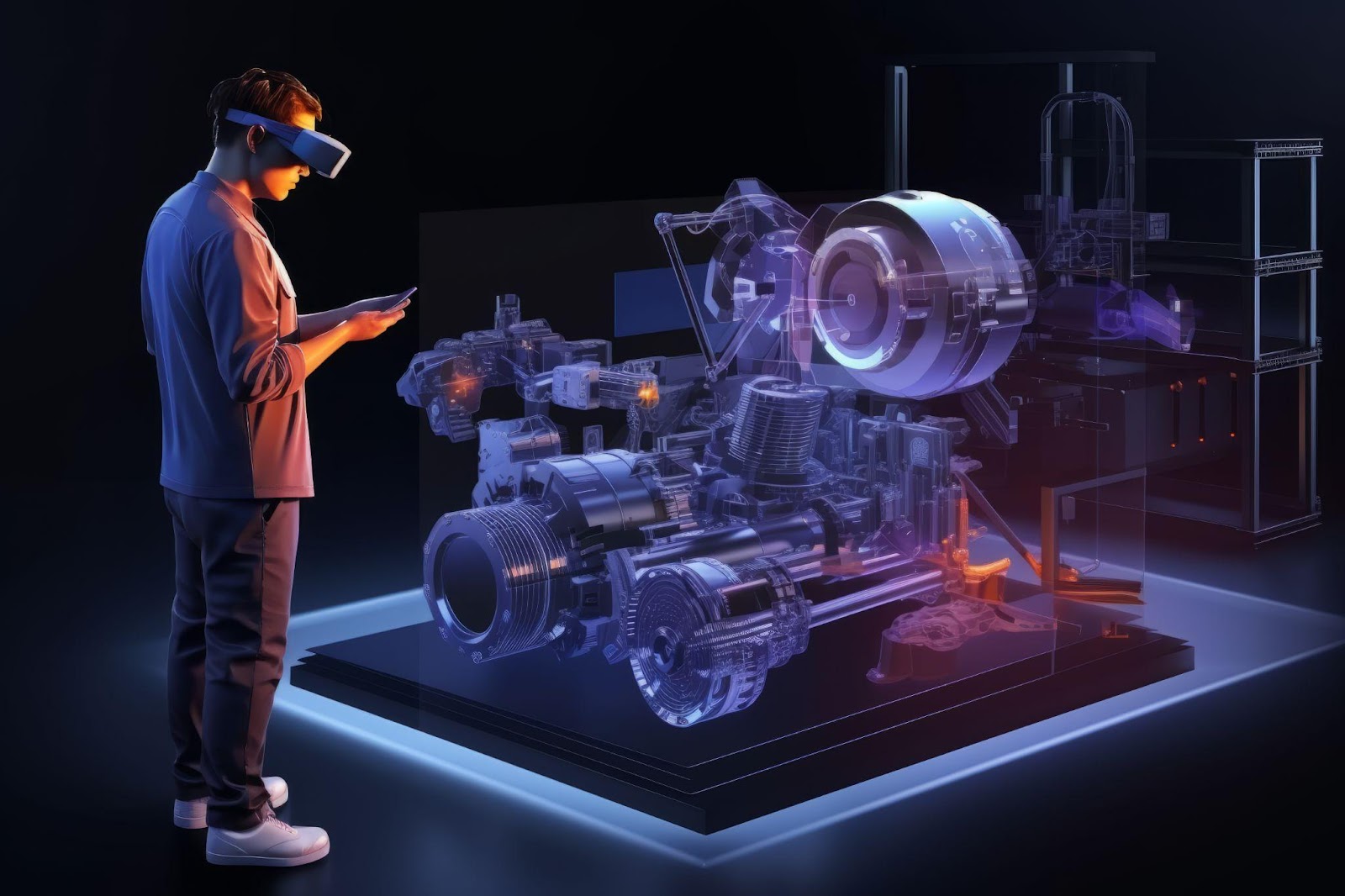
Determined to find a better way, Jacob turned to Simulation Powered Learning (SPL), a platform designed to build real-world project management capabilities through experiential learning.
With SPL, engineers and managers could:
- Simulate full project lifecycles, from kickoff to delivery, in realistic business contexts
- Make high-stakes decisions and experience the consequences in a controlled environment
- Improve cross-functional collaboration, time management, and problem-solving under pressure
Within months of implementation, SPL changed everything. New hires entered projects with confidence. They understood timelines, risk management, communication, and stakeholder handling, not just in theory, but through hands-on simulations tailored to real challenges.
Revolutionizing workforce training with immersive learning
Jacob’s story is common in manufacturing: theoretical training leaves new engineers unprepared for real-world execution, leading to costly mistakes, delays, and strained client relationships. His experience highlights the need for hands-on, immersive training to ensure engineers are job-ready before stepping onto the production floor.
By implementing SPL, Jacob’s company transformed its training with custom simulations tailored to real business challenges. Unlike generic project management courses or static e-learning, SPL offers immersive, experiential learning that actively engages engineers in real-world scenarios. With a single simulation score, companies can now measure training effectiveness and ensure workforce readiness.
Backed by a proven track record with large enterprises like Northrop Grumman, SPL enables rapid deployment within just three months, ensuring businesses see immediate impact. Additionally, SPL’s Train the Trainer program empowers internal teams to scale training effectively.
Don’t let outdated training hold your team back. Upgrade to SPL and empower your employees with hands-on learning that delivers measurable success.
Powered by MarketEngine from StartupWind